Understanding Regulatory, Quality, and Post-Market Requirements for OTC Drug Submissions: U.S. and India
- Trinity M Consulting
- Sep 24, 2024
- 4 min read
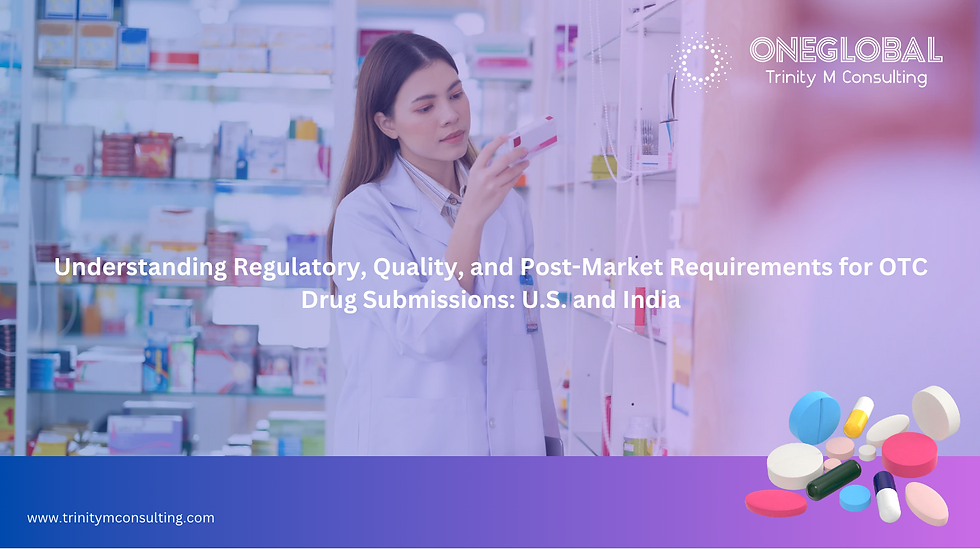
Bringing an Over-the-Counter (OTC) drug to market requires navigating complex regulatory frameworks to ensure product safety, efficacy, and compliance with local laws. For companies looking to submit an OTC drug application in both the U.S. and India, understanding the unique regulatory requirements in each country is essential. In this blog, we will outline the key requirements for OTC drug submissions in both the U.S. (FDA) and India, with a focus on regulatory, quality, and post-market obligations. Whether you're expanding your product globally or targeting a specific market, we hope this guide will help you streamline your submission process.
U.S. Regulatory Requirements for OTC Drug Submissions
In the United States, the FDA has a structured framework for OTC drug submissions under the New Drug Application (NDA) process. Here’s a breakdown of the core regulatory, quality, and post-market requirements:
Regulatory Requirements for the U.S.:
Marketing Authorization Application Forms (Form FDA 356h):
The Form FDA 356h is a critical part of the submission, containing detailed information about the product, including its formulation, the applicant, and the manufacturing process.
Regulatory Cover Letters:
A formal letter summarizing the application’s purpose, the type of submission (e.g., NDA, ANDA), and detailed product information. It serves as an introductory overview for the FDA reviewers.
Labeling (Product Labels, Inserts, Carton Labels):
Complete labeling must include essential details such as dosage instructions, active ingredients, warnings, and usage directions. For OTC products, accurate labeling helps consumers make informed decisions.
Patent Certification:
A certification declaring the status of patents related to the product. This may involve acknowledging patent expiration, non-applicability, or disputing a patent’s validity.
Quality and Manufacturing Requirements for the U.S.:
Chemistry, Manufacturing, and Controls (CMC):
The CMC section provides data on the drug substance and product, including the manufacturing process, batch production details, and quality control methods.
Stability Testing and Results:
Stability studies are crucial for determining shelf life and storage conditions. The results must be submitted to demonstrate the drug’s safety and efficacy over time.
Good Manufacturing Practices (GMP) Compliance Documentation:
Evidence that the manufacturing facilities follow Good Manufacturing Practices (GMP) guidelines, which are vital for ensuring product quality and consistency.
Nonclinical Studies:
Nonclinical pharmacology and toxicology reports that demonstrate the safety of the product through animal studies or other non-human testing.
Post-Market Requirements for the U.S.:
Adverse Event Reporting (AERS):
A system for collecting and reporting adverse events after the product is launched. The FDA monitors this to ensure ongoing safety.
Risk Management Plan (RMP):
A plan detailing how the company will identify, evaluate, and mitigate potential risks associated with the product once it’s on the market.
Post-Market Surveillance Plan:
Continuous monitoring of the product’s safety and effectiveness through real-world data collection and reporting.
India's Regulatory Requirements for OTC Drug Submissions
In India, the Central Drugs Standard Control Organization (CDSCO) is responsible for the approval and regulation of OTC drugs. The process for submitting an OTC drug in India differs from the U.S. in several key areas, particularly in labeling and compliance with specific local regulations.
Regulatory Requirements for India:
Application for Manufacturing and Marketing Authorization:
In India, companies must submit an application to the CDSCO, including details of the drug, its formulation, and manufacturing processes.
Drug Master File (DMF):
A comprehensive document that contains detailed information on the manufacturing, processing, packaging, and storage of the drug substance and product.
Labeling Requirements (As per Drugs and Cosmetics Act):
In India, labeling is governed by the Drugs and Cosmetics Act, 1940. Labels must include warnings, directions for use, and dosage instructions in both English and Hindi, and packaging must comply with Indian labeling standards.
Patent Certification and Compliance:
Like in the U.S., companies must certify that they comply with Indian patent laws. However, India follows a slightly different patent regime, so companies must navigate these legal frameworks carefully.
Quality and Manufacturing Requirements for India:
Good Manufacturing Practices (GMP) Compliance:
Compliance with India’s Schedule M of the Drugs and Cosmetics Act, which outlines GMP requirements for the manufacturing of drugs.
Pharmacopoeial Standards:
Indian pharmacopoeial standards must be adhered to, including specific quality tests for drug substances and products. The CDSCO may require additional product testing by local laboratories.
Stability Testing:
Stability testing must be conducted under climatic conditions specified for India (Zone IV), to ensure the product remains stable in the country’s diverse climatic regions.
Nonclinical Study Data:
For OTC drugs, data from nonclinical studies must be included, showing the product’s safety. India’s regulatory authorities may accept some foreign data, but locally conducted studies may be required in certain cases.
Post-Market Requirements for India:
Adverse Event Reporting:
Companies must establish a system for reporting adverse drug reactions to the CDSCO. India’s Pharmacovigilance Programme (PvPI) ensures safety monitoring of all marketed products.
Risk Management Plan (RMP):
Similar to the U.S., Indian authorities require an RMP to identify and mitigate risks throughout the product lifecycle.
Post-Marketing Surveillance:
Ongoing surveillance to ensure the product's safety and efficacy through real-world data collection. Companies are required to submit periodic reports on the drug’s performance in the market.
Key Differences Between the U.S. and India for OTC Submissions
While the core elements of regulatory and quality compliance remain similar, some key differences between the U.S. and India’s requirements include:
Labeling: In India, labeling must meet specific linguistic and packaging requirements under the Drugs and Cosmetics Act, while the U.S. requires compliance with FDA labeling guidelines.
Stability Testing: India’s unique climatic conditions mean that stability testing must be conducted under Zone IV conditions, while the U.S. follows its own climatic stability zones.
Pharmacopoeial Standards: In India, drug products must adhere to the Indian Pharmacopoeia, which may differ from the standards set by the U.S. FDA.
Conclusion
Successfully navigating OTC drug submissions in both the U.S. and India requires a deep understanding of each country’s regulatory framework. While there are many similarities, the differences in labeling, manufacturing practices, and post-market surveillance must be carefully managed to ensure compliance.
At OneGlobal Trinity M Consulting, we specialize in helping companies streamline their regulatory submissions for both U.S. and international markets, including India. Our expert team provides tailored solutions for ensuring compliance with FDA, CDSCO, and other regulatory bodies, guiding you through the complexities of both markets.
Need help with your OTC drug submission? Contact us today to learn how we can support your regulatory, quality, and post-market requirements in both the U.S. and India.
Comments